Streamlining production while maintaining quality has become imperative for manufacturers competing in today’s landscape. Assembling products faster allows companies to meet rising demand, drive down costs, and boost profitability. However, accelerating manual assembly processes often erodes accuracy through defects and rework. The solution lies in targeted automation using technologies like component feeder systems and power fastening tools. When appropriately integrated, this equipment removes bottlenecks, errors, and inefficiencies from the equation – driving throughput, consistency and output value higher.
The True Cost of Loose Hardware
Plants reliant on old-fashioned bins of jumbled fasteners may fail to recognize the chaos burden on total operating costs. Beyond paying purchasing staff to manually sort bulk orders into makeshift containers, consider the frequent production interruptions from working with low-tech screw storage:
- Workers fumbling to locate the right sizes & types = Lost Minutes
- Contamination from dirt/damage = Line Delays
- Inconsistent Quality = Rework & Rejects
- Misplaced/Missing Hardware = Downtime From Shortages
- Incorrect Installation = Wasted Material & Time
Now multiply similar inefficiencies across multiple shift changes daily. What may appear like minor productivity brakes or quality hiccups actually bleed significant efficiency over weeks and months. Loose hardware handling is far costlier than it appears!
Thankfully, advanced screw feeding equipment eliminates these issues through automation and mistake-proofing. Intelligent feeders recoup expenses rapidly, but more on that later. First, let’s tackle sluggish manual fastening processes hindering assembly pace and accuracy.
The Fatigue Factor Hammering Productivity
Overworked staff struggle with tedious fastening tasks. Their hands tire from forceful motions securing joint after joint. Small electronics have thousands of minute screws while massive truck components require bearing down with all one’s might. Surely an installer’s back, wrists and shoulders ache after hours hunched applying primitive mechanical advantage!
Without power tools assisting, screw driving rates decline over shifts – a documented phenomenon studied in depth. People are not designed for repeated high-exertion motions. Output inevitably downshifts as staff conserve energy to simply make it to quitting time. Unless…automation helps multiply production?
Impact Power Multiplies Throughput
Now envision that same worker operating an electric impact wrench. These high-torque rotary tools use compressed air or battery power to spin driver bits at extreme speeds – easily running down lag bolts in seconds without sweat. What took 30 seconds of intense effort manually now takes 2 seconds without stress. This allows installers to bolt widgets far faster with less fatigue.
Assuming a 60% reduced operation time, staff could theoretically install 90 more screws per hour. At ~$50 per employee hourly with benefits, that’s $45 of added value per person. Across 10 line assemblers over two shifts per day for 20 days a month, we’re looking at $180,000 increased productivity value from just this one process upgrade.
And unlike air tools which require costly compressors, rechargeable battery packs minimize infrastructure. Assemblers enjoy ergonomic assistance securing parts precisely together at maximum repeatable torque values without over or under tightening. Impact wrenches are force multipliers – amplifying returns on labor exponentially. Let’s keep exploring efficiency gains…
Component Feeders – Serving Production Non-Stop
Plant managers would cringe watching staff scour piles for hardware 30-40% of work time. Yet this remains reality for companies relying on unstructured boxes/bowls of fasteners. Workers digging for the next widget represents zero value-add while actual installation does. How can automation help?
Intelligent screw feeding systems continually orient and deliver components to points of use via vibratory bowls. Supplying production lines with orderly, mistake-proof parts accessibility minimizes the wasted moments between installation steps. These in-line presenting feeders keep operators building nonstop versus fetching loose items from chaotic bulk.
Setup changeovers take only seconds by swapping pre-filled bowls rather than hand sorting small items. Dispensed screws align perfectly for ready retrieval without manual inspection thanks to integrated cameras and scales. Not only does automation accelerate assembly by eliminating supply disruptions, advanced feed verification prevents defective parts from ever reaching workers – eliminating quality escapes.
Assuming screw presentation auto-feeding allows just 30 extra installs per operator per shift, that again equals big throughput gains quickly covering equipment costs. And the benefits keep growing over time without added overhead, driving down true unit costs across higher volumes. This lets manufacturers economically scale production at need to capture greater market share without deformation issues that arise when pushing human performance limits.
Flexible Assembly Delivers Top Efficiency
The examples illustrate how automation technologies like component feed systems and power tools boost productivity, quality, and labor ROI across assembly processes. As specialists in process design, Flexible Assembly prescribes the latest innovations best suited for the problem at hand:
- Intelligent Screw Feeders w/ Vision Inspection
- Digital Torque Analyzers and Power Drivers
- Mistake-Proof Assembly Fixtures
- Rapid Changeover Equipment
- Cost-Saving Electromagnets
- Gravity Replenishment Conveyors
Our tailor-made solutions consistently generate efficiency gains by driving out wasteful chaos and variability while preventing defects. Maximizing throughput means studying not just isolated steps but understanding how procedures interact across complex manufacturing flows.
Contact Flexible Assembly today to discuss how upgrading key bottlenecks with strategic automation can pay rapid dividends. Our expertise takes the guesswork out of “smart” equipment investments by ensuring the highest value impact.
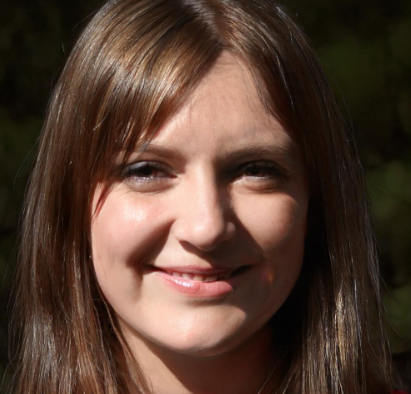
Melody Roth, a seasoned blog writer with a passion for the delectable world of food, specializes in crafting mouth-watering articles on favorites like pizza and burgers. With years of experience under her belt, Melody serves up stories as tantalizing as the dishes she describes, making her an invaluable voice in the culinary blogging realm.